Al Hamly General Contracting supplies Corrosion
Resistant Coatings for Air Handling Equipments. What is it, that
makes Al Hamly Group's Corrosion resistant coatings superior to that
of the others.....
Corrosion is nowadays widely accepted to be the
main cause of an early deterioration of heat exchanging coils, the
most vulnerable part of air sided HVAC equipment. If corrosion
occurs and pollution will adhere, without any corrective or
preventive measurements the performance will decrease by up to 80%
in some scenarios.
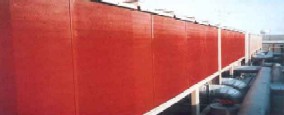
Technical - Information
The two most common forms of corrosion occurring
in HVAC/R equipment are known as galvanic corrosion and climate
impact corrosion. Each of these corrosions can lead to equipment
failure.
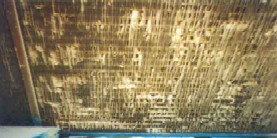
Corroded coil due to lack of protective treatment
Galvanic Corrosion
When dissimilar metals are electrically connected
in the presence of an electrolyte, a reaction occurs. this reaction
is known as galvanic corrosion. There must be a bi-metallic coupling
between two dissimilar metals in the presence of an electrolyte
solution, without these ingredients, there exists a risk of galvanic
corrosion. Galvanic corrosion most often causes degradation, which
may ultimately lead to destruction of the coil. Galvanic corrosion
of the unprotected coil begins at the bi-metallic coupling between
copper tube and the metallic fin. Consumption of the fin continues
until the coil performance is affected and severe visual
deterioration results.
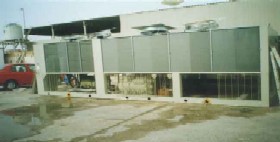
Coil protected from corrosion by use of special treatment
Climate Impact Corrosion
The corrosion caused by a reaction with the
environment, such as oxidation and chemical attack by the
environment. Copper will be affected by sulphur containing gases.
the result is a formation of a no protective layer on the metallic
surface, which will continue until the performance of the machine
does not meet the requirements. Unprotected copper in industrial
environments will lead to failure of the refrigeration system.
Sulphur and nitrogen are often the initiators of the corrosion
process.
A wide range of solutions is offered to protect
the heat exchanging elements from corroding. The price must not
exceed the performance of a coil protection, however the quality of
the solution varies from 'for ever lasting' to 'cosmetic solutions.'
To come to a presentation on the facts of coil
corrosion and the possible solution we would like to asses the
different exposure possibilities. Different circumstances call for
different solutions. Potentially corrosive outdoor environments
include areas to the sea coast, industrial sites, heavily populated
urban areas, some rural locations, or a combination of any of these
environments. In air handling applications, some indoor environments
such as swimming pool areas, water treatment facilities, and
industrial process areas can produce corrosive atmospheres.
Marine
Many emerging HVAC markets have a majority of
their populations located in coastal areas. This leads to an
increased number of air-conditioning applications located in
potentially corrosive environments. Coastal or marine environments
are characterized by the abundance of sodium chloride (salt) which
is carried by sea spray, mist or fog. Most importantly, this salt
water can be carried as for away as 5 miles from the coast. Even if
the HVAC equipment is a substantial distance from the ocean,
corrosion from salt water contamination can still occur if the
equipment is not properly protected. Line-of-sight distance from the
ocean, prevailing wind direction, relative humidity, wet/dry time,
and coil temperature will determine the severity of corrosion
potential in the coastal environment. As a result, the following
should be considered when the potential for coastal contamination
exists:
Is the unit within 5 miles of the ocean?
Visit the proposed installation sight. Is the
ocean visible from the building roof or outdoor mechanical area? If
so, the potential for severe coastal corrosion should be expected
and appropriate protection is strongly recommended.
Will the condenser coil face the ocean?
If the the condenser coil faces the ocean or
faces into the prevailing winds from the coast, there is high
probability of sea water contamination. appropriate protection is
strongly recommended.
If there is corrosion on the exterior
structures, other HVAC equipment, or other equipment with dissimilar
metals?
Look around the installation sites and the
surrounding areas. If there is evidence of corrosion, chances are
high that coastal corrosion exists and suitable protection is
required.
Industrial
Industrial applications are associated with a
host of diverse conditions, with the potential to produce various
atmospheric emissions. Sulphur and nitrogen oxide contaminants are
most often linked to industrial and high density urban environments.
Combustion of coal and fuel oils release sulphur oxides (SO2, SO3)
and nitrogen oxides (NOx) into the atmosphere. these gases
accumulate in the atmosphere and return to the ground in the form of
acid rain or low pH dew. Not only are industrial emissions
potentially corrosive, many industrial dust particles can be laden
with the harmful metal oxides, chlorides, sulphates, carbon
compounds. These particles, in the presence of oxygen, water, or
high humidity environments can be highly corrosive.
Combination Marine/Industrial
Salt-laden sea water mist, combined with the
harmful emissions of an industrial environment, pose a severe threat
to HVAC equipment life. the combined effect of salt mist and
industrial emission can accelerate corrosion. this environment
requires superior corrosion resistant properties for air
conditioning components to maintain optimum level of product
quality. Complete encapsulation of the coil surface and all copper
construction is recommended.
Urban
Highly populated areas generally have high levels
of automobile emissions and increased rates of building heating fuel
combustion. both conditions elevate sulphur oxides and nitrogen
oxides concentrations. Corrosion severity in this environment is a
function of the pollution levels which in turn depend upon several
factors including population density for the area. Any HVAC
equipment installed immediately adjacent to diesel exhaust,
incinerator discharge stacks, fuel burning boiler stacks, or areas
exposed to fossil fuel combustion emissions must be considered an
industrial application.
The solution to all these problems........
HERESITE VR-500 SERIES AIR DRY PHENOLIC
COATINGS
Generic Type: Air drying phenolic
Recommended usage: Heresite VR-500 air dry phenolic series coatings
are specially formulated to permit applications by brush, spray or
roller. Some of their outstanding properties are excellent
durability, good adhesion, good film building characteristics and
flexibility. When thoroughly aged, they produce hard corrosion
resistant films. Recommended as a heavy duty maintenance coating for
exposures to splash, spillage and fumes.
Successful applications include: agricultural
implements, chemical plants, canning factories, construction
equipment, marine finishes, steel plants, sewage disposal plants,
textile industry, underground and underwater service and ventilating
systems. The VR-514 brown coating is a primer finish combination
material, specially formulated for salt water service. |